CHAPTER 1 GENERAL INFORMATION, EQUIPMENT DESCRIPTION, AND THEORY OF OPERATION FOR MULTI-TEMPERATURE REFRIGERATED CONTAINER SYSTEM (MTRCS)MULTI-TEMPERATURE REFRIGERATED CONTAINER SYSTEM (MTRCS) GENERAL INFORMATIONFigure 1. MTRCS.MAINTENANCE FORMS, RECORDS, AND REPORTSNOMENCLATURE CROSS-REFERENCE LISTNOMENCLATURE CROSS-REFERENCE LIST CONTINUEDNOMENCLATURE CROSS-REFERENCE LIST CONTINUEDNOMENCLATURE CROSS-REFERENCE LIST CONTINUEDNOMENCLATURE CROSS-REFERENCE LIST CONTINUEDNOMENCLATURE CROSS-REFERENCE LIST CONTINUEDLIST OF ACRONYMS/ABBREVIATIONSLIST OF ACRONYMS/ABBREVIATIONS CONTINUEDLIST OF ACRONYMS/ABBREVIATIONS CONTINUEDLIST OF ACRONYMS/ABBREVIATIONS CONTINUEDQUALITY OF MATERIALTable 1. Location and Description of MTRCS Front View Components.Table 1. Location and Description of MTRCS Front View Components Continued.Figure 1. MTRCS Front View (Sheet 2 of 2).Table 2. Location and Description of MTRCS Rear View Components.Table 3. Location and Description of MTRCS Right Side View Components.Table 4. Location and Description of MTRCS Left Side View Components.Table 5. Location and Description of MTRCS Interior Left Wall Components.Table 6. Location and Description of MTRCS Interior Right Wall Components.Table 7. MTRCS System Specifications.Table 7. MTRCS System Specifications Continued.MULTI-TEMPERATURE REFRIGERATED CONTAINER SYSTEM (MTRCS) THEORY OF OPERATIONINSULATED CONTAINEREmergency Escape HatchesTable 1. Power Box Assembly Configuration for External Power.Figure 3. Control Box.Figure 4. Microprocessor Controller Display.Figure 5. Evaporators.Figure 6. CPR Valve.Figure 7. Accumulator.Figure 8. Compressor Unloader.DIESEL ENGINEFigure 10. Water Temperature Sensor.Figure 11. Cooling System.Figure 12. Engine Air Cleaner.Figure 14. Fuel Filter.ELECTRICAL DESIGN, CABLES, LIGHTING, ALARM, TEMPERATURE CONTROL, AND RECORDINGCHAPTER 2 TROUBLESHOOTING PROCEDURES FOR MULTI-TEMPERATURE REFRIGERATED CONTAINER SYSTEM (MTRCS)Table 1. Crew Troubleshooting Malfunction/Symptom Index.Figure 1. Relay Pin Out and Schematic.Table 2. Maintainer Maintenance Troubleshooting Malfunction/Symptom Index.Table 3. Sensor Voltage Chart for Suction Pressure Transducer.Table 4. Sensor Resistance Chart for Air Temperature, Return Air, Supply Air, and Water Temperature Sensor - ContinuedInitial SetupTable 1. Microprocessor Control Box Component Identification for Model MTRCS01.Table 1. Microprocessor Control Box Component Identification for Model MTRCS01 Continued.Figure 1. Microprocessor Control Box Back Wall and Bottom (Model MTRCS01).Figure 2. Microprocessor Control Box Door and Forward Wall (Model MTRCS01).Figure 3. Microprocessor Control Box Aft Wall (Model MTRCS01).Table 2. Microprocessor Control Box Component Identification for Model MTRCS02.Figure 3.1. Microprocessor Control Box Back Wall and Bottom (Model MTRCS02).Figure 3.2. Microprocessor Control Box Door (Model MTRCS02).Figure 4. Engine Will Not Start.Figure 5. Fault AL8 (STARTER) (Sheet 1 of 2).Figure 5. Fault AL8 (STARTER) (Sheet 2 of 2).Figure 6. Fault AL0 (ENG OIL) (Sheet 1 of 2).Figure 6. Fault AL0 (ENG OIL) (Sheet 2 of 2).Figure 7. Fault AL1 (ENG HOT) (Sheet 1 of 6).Figure 7. Fault AL1 (ENG HOT) (Sheet 2 of 6).Figure 7. Fault AL1 (ENG HOT) (Sheet 3 of 6).Figure 7. Fault AL1 (ENG HOT) (Sheet 4 of 6).Figure 7. Fault AL1 (ENG HOT) (Sheet 5 of 6).Figure 7. Fault AL1 (ENG HOT) (Sheet 6 of 6).Figure 8. Fault AL2 (HI PRESS) (Sheet 1 of 3).Figure 8. Fault AL2 (HI PRESS) (Sheet 2 of 3).Figure 8. Fault AL2 (HI PRESS) (Sheet 3 of 3).Figure 9. Fault AL3 (STARTFAIL) (Sheet 1 of 6).Figure 9. Fault AL3 (STARTFAIL) (Sheet 2 of 6).Figure 9. Fault AL3 (STARTFAIL) (Sheet 3 of 6).Figure 9. Fault AL3 (STARTFAIL) (Sheet 4 of 6).Figure 9. Fault AL3 (STARTFAIL) (Sheet 5 of 6).Figure 9. Fault AL3 (STARTFAIL) (Sheet 6 of 6).SERVICE AND FIELD MAINTENANCE REFRIGERATION UNIT TROUBLESHOOTING PROCEDURES (FAULT CODES AL4 AL7, AL9 AL15)Figure 1. Fault AL4 (LOW BATT).Figure 2. Fault AL5 (HIGH BATT).Figure 3. Fault AL6 (DEFRFAIL).Figure 4. Fault AL7 (ALT AUX).Figure 5. Fault AL9 (1RA SENSOR).Figure 6. Fault AL10 (2RA SENSOR).Figure 7. Fault AL11 (WT SENSOR).Figure 8. Fault AL12 (HIGH CDT) (Sheet 1 of 4).Figure 8. Fault AL12 (HIGH CDT) (Sheet 2 of 4).Figure 8. Fault AL12 (HIGH CDT) (Sheet 3 of 4).Figure 8. Fault AL12 (HIGH CDT) (Sheet 4 of 4).Figure 9. Fault AL13 (CD SENSOR).Figure 10. Fault AL14 (SBY MOTOR) (Sheet 1 of 2).Figure 10. Fault AL14 (SBY MOTOR) (Sheet 2 of 2).Figure 11. Fault AL15 (FUSE BAD).Figure 12. Fault AL15 (FUSE BAD) F4 (Sheet 1 of 2).Figure 12. Fault AL15 (FUSE BAD) F4 (Sheet 2 of 2).Figure 13. Fault AL15 (FUSE BAD) F5.Figure 14. Fault AL15 (FUSE BAD) F7 (Sheet 1 of 4).Figure 14. Fault AL15 (FUSE BAD) F7 (Sheet 2 of 4).Figure 14. Fault AL15 (FUSE BAD) F7 (Sheet 3 of 4).Figure 14. Fault AL15 (FUSE BAD) F7 (Sheet 4 of 4).Figure 15. Fault AL15 (FUSE BAD) F8 (Sheet 1 of 4).Figure 15. Fault AL15 (FUSE BAD) F8 (Sheet 2 of 4).Figure 15. Fault AL15 (FUSE BAD) F8 (Sheet 3 of 4).Figure 15. Fault AL15 (FUSE BAD) F8 (Sheet 4 of 4).SERVICE AND FIELD MAINTENANCE REFRIGERATION UNIT TROUBLESHOOTING PROCEDURES (FAULT CODES AL17 AL23)Figure 1. Fault AL17 (DISPLAY).Figure 2. Fault AL20 (1RA OUT) (Sheet 1 of 6).Figure 2. Fault AL20 (1RA OUT) (Sheet 2 of 6).Figure 2. Fault AL20 (1RA OUT) (Sheet 3 of 6).Figure 2. Fault AL20 (1RA OUT) (Sheet 4 of 6).Figure 2. Fault AL20 (1RA OUT) (Sheet 5 of 6).Figure 2. Fault AL20 (1RA OUT) (Sheet 6 of 6).Figure 3. Fault AL21 (2RA OUT) (Sheet 1 of 6).Figure 3. Fault AL21 (2RA OUT) (Sheet 2 of 6).Figure 3. Fault AL21 (2RA OUT) (Sheet 3 of 6).Figure 3. Fault AL21 (2RA OUT) (Sheet 4 of 6).Figure 3. Fault AL21 (2RA OUT) (Sheet 5 of 6).Figure 3. Fault AL21 (2RA OUT) (Sheet 6 of 6).Figure 4. Fault AL23 (NO POWER).Figure 5. Refrigeration Unit Runs But Will Not Heat (Sheet 1 of 11).Figure 5. Refrigeration Unit Runs But Will Not Heat (Sheet 2 of 11).Figure 5. Refrigeration Unit Runs But Will Not Heat (Sheet 3 of 11).Figure 5. Refrigeration Unit Runs But Will Not Heat (Sheet 4 of 11).Figure 5. Refrigeration Unit Runs But Will Not Heat (Sheet 5 of 11).Figure 5. Refrigeration Unit Runs But Will Not Heat (Sheet 6 of 11).Figure 5. Refrigeration Unit Runs But Will Not Heat (Sheet 7 of 11).Figure 5. Refrigeration Unit Runs But Will Not Heat (Sheet 8 of 11).Figure 5. Refrigeration Unit Runs But Will Not Heat (Sheet 9 of 11).Figure 5. Refrigeration Unit Runs But Will Not Heat (Sheet 10 of 11).Figure 5. Refrigeration Unit Runs But Will Not Heat (Sheet 11 of 11).Figure 6. No Microprocessor Display (Sheet 1 of 7).Figure 6. No Microprocessor Display (Sheet 2 of 7).Figure 6. No Microprocessor Display (Sheet 3 of 7).Figure 6. No Microprocessor Display (Sheet 4 of 7).Figure 6. No Microprocessor Display (Sheet 5 of 7).Figure 6. No Microprocessor Display (Sheet 6 of 7).Figure 6. No Microprocessor Display (Sheet 7 of 7).MULTI-TEMPERATURE REFRIGERATED CONTAINER SYSTEM (MTRCS) INITIAL SETUPFigure 1. Compartment 1 Evaporator Has No, or Limited, Airflow (Sheet 1 of 9).Figure 1. Compartment 1 Evaporator Has No, or Limited, Airflow (Sheet 2 of 9).Figure 1. Compartment 1 Evaporator Has No, or Limited, Airflow (Sheet 3 of 9).Figure 1. Compartment 1 Evaporator Has No, or Limited, Airflow (Sheet 4 of 9).Figure 1. Compartment 1 Evaporator Has No, or Limited, Airflow (Sheet 5 of 9).Figure 1. Compartment 1 Evaporator Has No, or Limited, Airflow (Sheet 6 of 9).Figure 1. Compartment 1 Evaporator Has No, or Limited, Airflow (Sheet 7 of 9).Figure 1. Compartment 1 Evaporator Has No, or Limited, Airflow (Sheet 8 of 9).Figure 1. Compartment 1 Evaporator Has No, or Limited, Airflow (Sheet 9 of 9).Figure 2. Compartment 2 Evaporator Has No, or Limited, Airflow (Sheet 1 of 9).Figure 2. Compartment 2 Evaporator Has No, or Limited, Airflow (Sheet 2 of 9).Figure 2. Compartment 2 Evaporator Has No, or Limited, Airflow (Sheet 3 of 9).Figure 2. Compartment 2 Evaporator Has No, or Limited, Airflow (Sheet 4 of 9).Figure 2. Compartment 2 Evaporator Has No, or Limited, Airflow (Sheet 5 of 9).Figure 2. Compartment 2 Evaporator Has No, or Limited, Airflow (Sheet 6 of 9).Figure 2. Compartment 2 Evaporator Has No, or Limited, Airflow (Sheet 7 of 9).Figure 2. Compartment 2 Evaporator Has No, or Limited, Airflow (Sheet 8 of 9).Figure 2. Compartment 2 Evaporator Has No, or Limited, Airflow (Sheet 9 of 9).Figure 3. Both Compartment Evaporators Have No Airflow (Sheet 1 of 3).Figure 3. Both Compartment Evaporators Have No Airflow (Sheet 2 of 3).Figure 3. Both Compartment Evaporators Have No Airflow (Sheet 3 of 3).Figure 4. Standby Motor Will Not Come ON (NO ALARM) (Sheet 1 of 6).Figure 4. Standby Motor Will Not Come ON (NO ALARM) (Sheet 2 of 6).Figure 4. Standby Motor Will Not Come ON (NO ALARM) (Sheet 3 of 6).Figure 4. Standby Motor Will Not Come ON (NO ALARM) (Sheet 4 of 6).Figure 4. Standby Motor Will Not Come ON (NO ALARM) (Sheet 5 of 6).Figure 4. Standby Motor Will Not Come ON (NO ALARM) (Sheet 6 of 6).CHAPTER 3 MAINTAINER MAINTENANCE INSTRUCTIONS FOR MULTI-TEMPERATURE REFRIGERATED CONTAINER SYSTEM (MTRCS)MULTI-TEMPERATURE REFRIGERATED CONTAINER SYSTEM (MTRCS) SERVICE UPON RECEIPTPRELIMINARY SERVICE OF EQUIPMENTMULTI-TEMPERATURE REFRIGERATED CONTAINER SYSTEM (MTRCS) PMCS INTRODUCTIONCORROSION PREVENTION AND CONTROL (CPC)CLEANING AND LUBRICATIONMULTI-TEMPERATURE REFRIGERATED CONTAINER SYSTEM (MTRCS) PREVENTATIVE MAINTENANCE CHECKS AND SERVICES (PMCS)Table 1. Maintainer Maintenance Preventative Maintenance Checks and Services (PMCS) Continued.Table 1. Maintainer Maintenance Preventative Maintenance Checks and Services (PMCS) Continued.Table 1. Maintainer Maintenance Preventative Maintenance Checks and Services (PMCS) Continued.Table 1. Maintainer Maintenance Preventative Maintenance Checks and Services (PMCS) Continued.Table 1. Maintainer Maintenance Preventative Maintenance Checks and Services (PMCS) Continued.Table 1. Maintainer Maintenance Preventative Maintenance Checks and Services (PMCS) Continued.Table 1. Maintainer Maintenance Preventative Maintenance Checks and Services (PMCS) Continued.Table 1. Maintainer Maintenance Preventative Maintenance Checks and Services (PMCS) Continued.Table 1. Maintainer Maintenance Preventative Maintenance Checks and Services (PMCS) Continued.Table 1. Maintainer Maintenance Preventative Maintenance Checks and Services (PMCS) Continued.Table 1. Maintainer Maintenance Preventative Maintenance Checks and Services (PMCS) Continued.Table 1. Maintainer Maintenance Preventative Maintenance Checks and Services (PMCS) Continued.Table 1. Maintainer Maintenance Preventative Maintenance Checks and Services (PMCS) Continued.Table 1. Maintainer Maintenance Preventative Maintenance Checks and Services (PMCS) Continued.Table 1. Maintainer Maintenance Preventative Maintenance Checks and Services (PMCS) Continued.Table 1. Maintainer Maintenance Preventative Maintenance Checks and Services (PMCS) Continued.Table 1. Maintainer Maintenance Preventative Maintenance Checks and Services (PMCS) Continued.MAINTAINER MAINTENANCE FUEL TANK SERVICEFigure 1. Fuel Drain Cock.SERVICE CONTINUEDMULTI-TEMPERATURE REFRIGERATED CONTAINER SYSTEM (MTRCS) ACCESS PANELS REPLACEFigure 1. Top Panels Looking Down.Figure 2. Front Panel Assembly.Remove Right-Side PanelFigure 4. Left-Side Panel.Install Right-Side PanelInstall Front Panel Cover AssemblyMAINTAINER MAINTENANCE REFRIGERATION UNIT SERVICEPump Refrigeration Unit DownSERVICE CONTINUEDFigure 2. Receiver Outlet Valve.Figure 3. Control Panel.Release Refrigerant into SystemSERVICE CONTINUEDSERVICE CONTINUEDRefrigerant Leak CheckSERVICE - CONTINUEDSERVICE - CONTINUEDEvacuation and DehydrationSERVICE - CONTINUEDCharge System with RefrigerantSERVICE CONTINUEDSERVICE CONTINUEDEMERGENCY STOP SWITCH REPLACEFigure 2. Emergency Stop Switch.REPLACE CONTINUEDMAINTAINER MAINTENANCE COMPRESSOR SERVICECheck Compressor Oil LevelFigure 1. Compressor Oil Level Sight Glass (Typical).Adding Oil to Compressor in SystemFigure 2. Compressor Suction and Discharge Service Valves.Adding Compressor Oil Using Oil PumpAdding Oil to Replacement CompressorSERVICE CONTINUEDMAINTAINER MAINTENANCE COMPRESSOR UNLOADER VALVE COIL TEST, REPLACEFigure 1. Compressor Unloader Valve Test.TEST CONTINUEDThe compressor unloader valve solenoid coil can be replacedFigure 2. Compressor Unloader Valve Replace.MAINTAINER MAINTENANCE FILTER-DRIER TEST, REPLACEFigure 1. Filter-Drier Test.Replace a defective filter-drier as follows:Figure 2. Filter-Drier.REPLACE CONTINUEDHIGH PRESSURE CUTOUT SWITCH/PRESSURE CONTROL SWITCH TEST, REPLACEFigure 1. High Pressure Cutout Switch Test Setup.Replace either high pressure cutout switch, HP1 and HP2, as follows:Figure 2. HP1 and HP2.REPLACE CONTINUEDMAINTAINER MAINTENANCE COMPRESSOR SENSORS REPLACE, TESTFigure 1. Compressor Discharge Temperature Sensor.Figure 2. Suction Pressure Transducer.Figure 3. Starter Solenoid Wire.Figure 4. Microprocessor Controller Display.Compressor Discharge Temperature SensorSuction Pressure TransducerCONDENSER COIL INSPECT, SERVICEFigure 1. Condenser Coil Location.ServiceSERVICE CONTINUEDMAINTAINER MAINTENANCE COMPRESSOR PRESSURE REGULATING VALVE ADJUSTFigure 1. Compressor Pressure Regulating Valve Adjustment.ADJUST CONTINUEDSERVICE CONTINUEDFigure 1. Engine Oil Dipstick, Radiator Overflow, and Cap.'Unknown' by Unknown - Page 309 of 1084MAINTAINER MAINTENANCE OIL FILTER REPLACEFigure 1. Engine Oil Drain Hose Unclamped.REPLACE CONTINUEDReplace Oil FilterFigure 3. Engine Oil Filter.Add Engine OilREPLACE CONTINUEDREPLACE CONTINUEDMAINTAINER MAINTENANCE FUEL FILTER REPLACEFigure 1. Replace Fuel Filter.REPLACE CONTINUEDREPLACE CONTINUEDMAINTAINER MAINTENANCE COOLING SYSTEM SERVICE, REPAIRFigure 1. Drain Cooling System.SERVICE CONTINUEDFigure 2. Clean Cooling System.Flush Cooling SystemFigure 3. Flush Cooling System.SERVICE CONTINUEDFigure 4. Refill Cooling System.Replace Water PumpFigure 5. Water Pump Assembly Flange.Figure 6. Water Pump.REPAIR CONTINUEDReplace Water Pump Return HosesFigure 7. Water Pump Return Hose.Replace Water Pump Supply HoseFigure 8. Water Pump Supply Hose.MAINTAINER MAINTENANCE THERMAL WATER TEMPERATURE RESISTOR REPLACEFigure 2. Emergency Stop Switch.Figure 3. Thermal Water Temperature Resistor.Figure 4. POWER ON/DOWN Switch.MAINTAINER MAINTENANCE THERMOSTAT REPLACEFigure 2. Emergency Stop Switch.Figure 3. Thermostat.REPLACE CONTINUEDREPLACE CONTINUEDMAINTAINER MAINTENANCE STARTER REPLACEFigure 2. Emergency Stop Switch.Figure 3. Starter.REPLACE - CONTINUEDMAINTAINER MAINTENANCE ALTERNATOR (MTRC 501 ONLY) TEST, REPLACEFigure 1. Battery Box.Figure 2. POWER ON/DOWN Switch.Figure 3. Emergency Stop Switch.REPLACE CONTINUEDREPLACE CONTINUEDREPLACE CONTINUEDREPLACE CONTINUEDMAINTAINER MAINTENANCE ALTERNATOR (MTRC 502 ONLY) TEST, REPLACEFigure 1. Battery Box.Figure 2. POWER ON/DOWN Switch.Figure 3. Emergency Stop Switch.Figure 4. Alternator Removal.REPLACE CONTINUEDREPLACE CONTINUEDREPLACE CONTINUEDMAINTAINER MAINTENANCE DIESEL ENGINE FUEL FEED PUMP SERVICE, REPLACESERVICE CONTINUEDFigure 2. Fuel Pump Service.SERVICE CONTINUEDFigure 3. POWER ON/DOWN Switch.Figure 4. Fuel Pump Removal.REPLACE CONTINUEDFigure 5. Fuel Pump Installation.REPLACE CONTINUEDMAINTAINER MAINTENANCE DIESEL ENGINE GLOW PLUGS TEST, REPLACEFigure 2. Emergency Stop Switch.Figure 3. Glow Plug Lead Assembly Test.TEST CONTINUEDFigure 4. Glow Plug Lead Assembly Replacement.REPLACE CONTINUEDMAINTAINER MAINTENANCE CONDENSER FAN REPLACEFigure 1. Emergency Stop Switch.Figure 2. Condenser Fan Removal (Sheet 1 of 2).Figure 2. Condenser Fan Removal (Sheet 2 of 2).REPLACE CONTINUEDFigure 3. Alternator Mounting Removal.Figure 4. Standby Motor Alignment Clearances.REPLACE CONTINUEDFigure 5. Condenser Fan Installation (Sheet 1 of 2).Figure 5. Condenser Fan Installation (Sheet 2 of 2).REPLACE CONTINUEDFigure 6. Alternator Mounting Installation.REPLACE CONTINUEDSTANDBY MOTOR TO SINGLE-PHASE ALTERNATOR V-BELT REPLACE, ADJUSTFigure 1. POWER ON/DOWN Switch.Figure 3. Alternator V-Belt.REPLACE CONTINUEDADUJST V-Belt Tension CheckFigure 4. V-Belt Tension Check.Figure 5. V-Belt Tension Gauge.Figure 6. POWER ON/DOWN Switch.Figure 7. Emergency Stop Switch.Figure 8. Alternator V-Belt.MAINTAINER MAINTENANCE STANDBY MOTOR TO COMPRESSOR V-BELT REPLACE, ADJUSTFigure 2. Emergency Stop Switch.Figure 3. Standby Motor to Compressor V-Belt.REPLACE CONTINUEDFigure 4. Standby Motor to Compressor V-Belt Tension.V-Belt Tension CheckFigure 5. V-Belt Tension Check.Figure 6. V-Belt Tension Gauge.ADJUST CONTINUEDV-Belt AdjustmentFigure 7. Standby Motor to Compressor V-Belt Tension.ADJUST CONTINUEDMAINTAINER MAINTENANCE ENGINE TO COMPRESSOR V-BELT REPLACE, ADJUSTFigure 1. POWER ON/DOWN Switch.Figure 3. Engine to Compressor V-Belt Idler.REPLACE CONTINUEDV-Belt Tension CheckADJUST CONTINUEDFigure 5. V-Belt Tension Gauge.V-Belt AdjustmentFigure 7. Emergency Stop Switch.ADJUST CONTINUEDMAINTAINER MAINTENANCE WATER PUMP V-BELT REPLACEFigure 3. Front Panel Cover.REPLACE CONTINUEDFigure 4. Water Pump V-Belt.REPLACE CONTINUEDFigure 5. V-Belt Tension Check.Figure 6. V-Belt Tension Gauge.REPLACE CONTINUEDMAINTAINER MAINTENANCE MUFFLER REPAIR, REPLACEFigure 1. POWER ON/DOWN Switch.Note the orientation of the rain cap before removing itFigure 3. Exhaust Manifold.REPAIR CONTINUEDREPLACE CONTINUEDFigure 4. Exhaust Manifold.REPLACE CONTINUEDFigure 1. POWER ON/DOWN Switch.Figure 2. Emergency Stop Switch.Figure 3. Oil Pressure Switch.Figure 4. Emergency Stop Switch.MAINTAINER MAINTENANCE RUN SOLENOID REPLACE, TESTFigure 2. Emergency Stop Switch.Figure 3. Run Solenoid Removal.Install Run SolenoidFigure 4. Run Solenoid Installation.Figure 5. Run Solenoid Test.MAINTAINER MAINTENANCE SPEED SOLENOID REPLACE, TESTFigure 2. Emergency Stop Switch.Figure 3. Speed Control Solenoid Removal.REPLACE CONTINUEDMAINTAINER MAINTENANCE EVAPORATOR BLOWER MOTOR REPLACEFigure 1. Control Panel Assembly.Figure 2. Evaporator Cover Removal.Figure 3. Evaporator Blower Motor Removal.Figure 4. Evaporator Blower Motor Installation.Figure 5. Evaporator Cover Installation.Figure 6. Control Panel Assembly.MAINTAINER MAINTENANCE EVAPORATOR BLOWER MOTOR CAPACITOR REPLACEFigure 1. Control Panel Assembly.REPLACE - CONTINUEDFigure 2. Evaporator Capacitor.MAINTAINER MAINTENANCE EVAPORATOR THERMOSTATIC EXPANSION VALVE INSPECTFigure 1. Control Box.Figure 2. Evaporator Thermostatic Expansion Valve.INSPECT CONTINUEDMAINTAINER MAINTENANCE HEATER REPLACEREPLACE CONTINUEDFigure 2. Heater Access.Figure 3. Heater.REPLACE CONTINUEDFigure 4. Heater Access.Figure 5. Control Box.MAINTAINER MAINTENANCE LIQUID SOLENOID VALVE COIL REPLACEFigure 1. Liquid Solenoid Valve Coil Replacement.REPLACE - CONTINUEDMAINTAINER MAINTENANCE HOT GAS VALVE COIL REPLACEFigure 1. Hot Gas Valve Coil Replacement.REPLACE CONTINUEDMAINTAINER MAINTENANCE EVAPORATOR SENSORS INSPECT, REPLACEFigure 1. Evaporator Sensors.Return Air SensorFigure 2. Return Air and Temperature Chart Recorder Sensors.Figure 3. Cable Routing.Figure 4. Wiring Disconnect.Figure 5. Ferrite Noise Suppressor.Figure 6. Cable Routing.Figure 7. Evaporator Sensors.21. On inside of container, carefully pull sensor (Figure 7, Item 5) and cableFigure 8. Chart Recorder Rear Cover.Defrost Thermistor Sensor (DTS)Figure 10. DTS Mounting Bolt.Figure 11. DTS Wire Splice.MAINTAINER MAINTENANCE DRAIN HOSES REPLACEFigure 1. Drain Hoses.Breather ElementsFigure 2. Breather.MAINTAINER MAINTENANCE LIGHTING REPLACEFigure 1. Light Strip Replace.Install Wall Mounted Light Strip Lamp AssembliesRemove Multi-Light Assembly White LED Light Strip LT3.Figure 2. Removal of White LT3 Light Strip.Install Multi-Light Assembly White LED Light Strip LT3.Figure 3. Installation of White LT3 Light Strip.Figure 4. Removal of Red BLT3 Light Strip.Install Multi-Light Assembly Red LED Light Strip BLT3.Figure 5. Installation of Red BLT3 Light Strip.Figure 6. Removal of White LT4 Light Strip.Install Multi-Light Assembly White LED Light Strip LT4.Figure 7. Installation of White LT4 Light Strip.MAINTAINER MAINTENANCE POWER CABLE ASSEMBLIES TEST, REPLACETest Cable Assembly P1AFigure 2. Switch S1 and S2 Contact Arrangement and Circuit Diagram.Figure 4. Cable Assembly P1A and Contact Arrangement.Test Cable Assembly P2AFigure 5. Cable Assembly P2A and Contact Arrangement.Test Cable Assembly P1BTable 3. Cable Assembly P1B.Figure 7. Cable Assembly P2B and Contact Arrangement.Replace Cable Assembly P1AFigure 9. Power Cable Assembly P1A Replacement.There are three ground wires attached to the power box GND1. Slide cord mesh (Figure 9, Item 12) over wires and onto replacement cable assemblyReplace Cable Assembly P2AFigure 10. Power Cable Assembly P2A Removal.REPLACE CONTINUED - Loosen TerminalREPLACE CONTINUED - InstallFigure 11. Power Cable Assembly P2A Installation.REPLACE CONTINUEDMAINTAINER MAINTENANCE BATTERY SERVICE, REPLACEFigure 1. Service of Battery.Reconnect Battery and Voltage CheckSERVICE CONTINUEDFigure 2. Voltage Check of Battery.5. Clean battery positive (+) (Figure 3, Item 5) and negative (-)Figure 3. Cleaning of Battery.1. Loosen and remove two lock nuts (Figure 4, Item 7) and two flat washersFigure 4. Removal/Installation of Battery.1. Install replacement battery (Figure 4, Item 1) in battery box (Figure 4, Item 2).MAINTAINER MAINTENANCE BATTERY JUMP START1. Loosen and remove two lock nuts (Figure 1, Item 2)If the MTRCS is being jumped from equipment with a 12VDC systemFigure 1. Battery.Figure 2. MTRCS Jump-Start Procedure.13. Allow good battery to charge in equipmentMAINTAINER MAINTENANCE TEMPERATURE CHART RECORDER TEST, REPLACEFigure 1. Temperature Chart Recorder.REPLACE CONTINUEDFigure 3. Evaporator Sensors.Figure 4. Temperature Chart Recorder Replacement.REPLACE CONTINUEDFigure 5. Evaporator Sensors.Figure 6. Cartridge Pen Arm Removal.Figure 7. Changing Cartridge Pen Arm.MAINTAINER MAINTENANCE DOCUMENT HOLDER REPLACE, REPAIRFigure 1. Document Holder.Replace Lid GasketsREPAIR CONTINUEDMAINTAINER MAINTENANCE MULTI-TEMPERATURE REFRIGERATED CONTAINER SYSTEM (MTRCS) REPAIRREPAIR CONTINUEDFigure 1. MTRCS Skin Patch Repair.REPAIR CONTINUEDReplace PLS Roller LanyardsReplace Swing Out Panels Lanyard, ClipsFigure 3. Swing Out Panel Lanyard and Clips.Topcoat Application Without Primer.Topcoat Application With Primer.REPAIR CONTINUEDMAINTAINER MAINTENANCE FUEL TANK REPLACE, REPAIRFigure 1. Fuel Tank.REPLACE CONTINUEDInstall Fuel TankReplace Liquid Level Gauge AssemblyFigure 2. Liquid Level Gauge.REPAIR CONTINUEDReplace Fuel Level Sending UnitFigure 3. Fuel Sending Unit.REPAIR CONTINUEDReplace Fuel Tank CapFigure 4. Fuel Cap/Filler Neck/Strainer.Replace Filler Neck Flange/StrainerREPAIR - CONTINUED Replace ElbowFigure 5. Fuel Tank Components.6. Apply sealant to threads of replacement elbowReplace Fuel Outlet AssemblyFigure 6. Fuel Tank Components.Replace Fuel Tank Drain HosesFigure 7. Fuel Tank Drain Hoses.MAINTAINER MAINTENANCE REFRIGERATION UNIT (MTRC 501 ONLY) REPLACEFigure 1. Electrical and Fuel Line Disconnects.6. Slightly above control panel assembly, tag and disconnect 50/60 Hz switchThe disconnect point of the braided line connectorFigure 4. Capacitor Box (P14/J14) and Power (P13/J13) Connectors.13. Tag and disconnect evaporator control connector (P8/J8)The ground wires for connectors 1CP and 2CPFigure 7. Refrigeration Lines.25. Loosen diesel engine muffler pipe U-bolt (Figure 8, Item 1)Figure 9. Radiator Cap.Figure 10. Electrical Cable Feeds.Figure 11. Support Angle Bolt Layout.30. Remove two bolts (Figure 12, Item 1), lock washers (Figure 12, Item 2), and washerFigure 13. Forklift Slots.Falling from the roof of the MTRCS can cause serious personal injuryFigure 14. Radiator Cap.Figure 15. Forklift Slots.7. While guiding cables in, slowly move forklift forward towards MTRCSFigure 17. Refrigeration Unit Mounting Bolts.Figure 18. Support Angle Bolt Layout.REPLACE CONTINUEDFigure 20. Refrigeration Lines.Figure 21. 1CP and 2CP Electrical Connectors.25. Reconnect evaporator control connector (P8/J8)Figure 23. Capacitor Box (P14/J14) and Power (P13/J13) Connectors.29. Connect braided line connector (P12/J12)32. Reconnect 50/60 Hz switch connector (P11/J11)Figure 26. Electrical and Fuel Line Connections.MAINTAINER MAINTENANCE REFRIGERATION UNIT (MTRC 502 ONLY) REPLACEFigure 1. Electrical and Fuel Line Disconnects.Figure 2. 50/60 Hz, P3/J3, and P9/J9 Electrical Connectors.Figure 3. Braided Line (P12/J12) and P6/J6 Connectors.Figure 4. Power (P13/J13) Connector.Figure 5. Evaporator Control Connector.Figure 6. 1CP and 2CP Electrical Connectors.Figure 7. Refrigeration Lines.Figure 8. Muffler Pipe U-Bolt.Figure 9. Radiator Cap.Figure 10. Electrical Cable Feeds.27. Unbolt support angle at front end near bale bar by removing three boltsFigure 12. Refrigeration Unit Mounting Bolts.Figure 13. Forklift Slots.32. Access top of MTRCS using roof access provided.Figure 14. Radiator Cap.Figure 15. Forklift Slots.Figure 16. Electrical Cable Feeds.Figure 17. Refrigeration Unit Mounting Bolts.Figure 18. Support Angle Bolt Layout.Figure 19. Muffler Pipe U-bolt.Figure 20. Refrigeration Lines.Figure 21. 1CP andFigure 22. Evaporator Control Connector.Figure 23. Power (P13/J13) Connector.Figure 24. Braided Line P12/J12 and P6/J6 Connectors.Figure 25. 50/60 Hz, P3/J3, and P9/J9 Electrical Connectors.Figure 26. Electrical and Fuel Line Connections.38. Reconnect battery (WP 0053, Reconnect). Tie wrap cables together.MAINTAINER MAINTENANCE COMPRESSOR REPLACEFigure 1. Refrigeration Support Bracket Removal.6. Partially remove alternator (WP 0030, Remove).Figure 2. Compressor Removal.Figure 3. Compressor Mounting Aft End.Figure 4. Compressor Hoist Install.31. Drain compressor oil into suitable container (WP 0016The two forward mount bolts will pass through the spacersFigure 5. Compressor Installation.23. Reconnect compressor discharge temperature sensor electrical connectorFigure 6. Refrigeration Support Bracket Installation.33. Perform evacuation and dehydration to 500 (± 25) micronsMAINTAINER MAINTENANCE COMPRESSOR PRESSURE REGULATING VALVE REPLACEFigure 1. CPR Valve.The accumulator will need to be loosened from its mounting position19. Reinstall refrigeration unit onto MTRCSMain Heat Solenoid ValveFigure 1. Main Heat Valve Coil.A very small coil alignment pin is located at top of the valve outer body.Main Heat Valve and 7/8-Inch Check Valve AssemblyFigure 2. Main Heat Valve Removal.Because of tight clearance, it may be necessary to cut half of pipeFigure 3. Heat Valve and Coil Installation.16. On replacement main heat valve (Figure 2, Item 20)32. Reconnect electrical connector to valve coilMAINTAINER MAINTENANCE RECEIVER PRESSURE SOLENOID VALVE REPAIR, REPLACEFigure 1. Receiver Pressure Solenoid Coil.Perform the replacement task only if repair is ineffective.Figure 2. Receiver Pressure Solenoid Valve.7. Desolder each end of 1/4-inch receiver pressure solenoidMAINTAINER MAINTENANCE DISCHARGE SERVIEC VALVE REPLACEFigure 1. Discharge Service Valve Removal.Many of the chemicals used while soldering are toxicFigure 2. Discharge Service Valve Installation.Many of the chemicals used while soldering are toxic.22. Install top-left panel (WP 0013, Install).MAINTAINER MAINTENANCE SUCTION SERVICE VALVE REPLACEFigure 1. Suction Service Valve Assembly Removal.Rear side of saddle clamp will stay in place until both saddle clamps have been removedFigure 2. Support Arm.Figure 3. Accumulator Mounting Removal.Figure 4. Suction Service Valve Assembly (Standalone).23. Install fitting (Figure 4, Item 4) in new valve (Figure 4, Item 1).Figure 5. Suction Service Valve Assembly Installation.36. Install support arm (Figure 3, Item 1) and support arm bracketMAINTAINER MAINTENANCE RECEIVER AND CHECK VALVES REPLACEFigure 1. Receiver.11. Remove cap screw securing back of receiver.Figure 2. Condenser to Receiver 3/8-Inch Check ValveFigure 2. Condenser to Receiver 3/8-Inch Check Valve Replacement.8. Carefully align piping (Figure 3, Item 2) with 1/4-inch check valveMAINTAINER MAINTENANCE CONDENSER REPLACEFigure 1. Lower Radiator Hose Disconnect.Figure 2. Upper Radiator Hose Disconnect.Figure 3. Overflow Tank.Figure 4. Channel Bars.Figure 5. Receiver Lines Disconnect.18. Remove one screw (Figure 6, Item 1), nut (Figure 6, Item 2), lock washerFigure 6. Clamp Removal at Filter-Drier.24. Remove screw (Figure 7, Item 4) securing hot gas valve coilFigure 8. Desolder Refrigerant Pipe.Figure 9. Discharge Service Valve and Line.There are four hex head bolts securing the base of the condenser assemblyThe condenser assembly weighs approximately 40 pounds and is a bulky item11. Install two clamps (Figure 6, Item 5) to two refrigerant pipesThe MTRCS contains high voltage sources and exposed rotating parts.MAINTAINER MAINTENANCE ACCUMULATOR/HEAT EXCHANGER REPLACEFigure 1. Support Arm.Due to the fragile nature of the accumulator neck flanges and the tight workspaceFigure 2. Accumulator/Heat Exchanger Removal.18. Desolder 1-1/8-inch refrigerant pipe (Figure 2, Item 24) between accumulatorFigure 3. Accumulator Buildup.29. Carefully remove accumulator without disturbing pipe alignment42. Install 3/8-inch refrigerant pipe fitting (Figure 4, Item 21)Figure 4. Accumulator/Heat Exchanger Installation.MAINTAINER MAINTENANCE SIGHT GLASS REPLACEREPLACE CONTINUEDMAINTAINER MAINTENANCE REFRIGERATION UNIT DIESEL ENGINE REPLACERefrigeration unit diesel engineFigure 2. Air Intake Manifold.Figure 3. Air Intake Cleaner.Figure 4. Water Pump Supply Hose Disconnect.Figure 5. Radiator Hose.Table 1. Engine Harness Disconnects.Figure 7. Engine Inlet and Outlet Fuel Lines.Figure 8. Oil Lines.Figure 9. Engine Ground Strap.Mounting bracket parts diagramFigure 11. Hoist Attachment Points.The engine fits tightly in the refrigeration unit chassisInstall the refrigeration unit diesel engine as follows:Mounting bracket parts breakdown11. Torque five bolts (Figure 12, Item 1) to 50 foot-poundsFigure 13. Engine Ground Strap.Figure 14. Oil Lines.Figure 15. Engine Inlet and Outlet Fuel Lines.Table 2. Engine Harness Connects.Figure 17. Radiator Hose.27. Secure wire harness (Figure 17, Item 2) to radiator return hose30. Perform Alignment per this WP.Alignment of the three major refrigeration unit componentsFigure 22. Outboard Engine Mount Bracket Bolts.9. Loosen five bolts (Figure 23, Item 1) on inboard engine mount bracketFigure 24. Alignment Clearances.15. Install top-right panel (WP 0013, Install).MAINTAINER MAINTENANCE IDLER PULLEY REPLACEFigure 1. Emergency Stop Switch.Belt Installation DiagramEngine to Compressor V-Belt IdlerFigure 3. Engine to Compressor V-Belt Idler.12. Install tensioner adjustment bolt (Figure 3, Item 1) and washer (Figure 3, Item 3)MAINTAINER MAINTENANCE ENGINE MOUNTED CENTRIFUGAL CLUTCH REPLACE8. Partially remove engine to compressor V-belt (Figure 1, Item 8)9. Immobilize flywheel (Figure 2, Item 3) by holding crankcase pulley14. Install idler assembly (Figure 1, Item 3) onto bracket (Figure 1, Item 4).MAINTAINER MAINTENANCE MICROPROCESSOR CONTROLLER ASSEMBLY REPLACE, SERVICEFigure 1. Controller.MAINTAINER MAINTENANCE ELECTRICAL BOX REPAIRFigure 1. Electrical Box Repair.Repair Replace ContactorFigure 2. Contactor Repair.MAINTAINER REPLACE STANDBY MOTOR/SINGLE-PHASE ALTERNATOR (MTRC 501 ONLY) REPLACEFigure 1. Standby Motor Electrical Connection.4. Remove standby motor to compressor V-belt (WP 0036, Remove).Alternator Installation DiagramBefore removing fan, mark a fan blade to note the orientationParts Breakdown of Motor with Fan Blade24. Lift standby motor/single-phase alternator assemblyFigure 4. Standby Motor/Single-Phase Alternator Assembly.Install - The radiator coils damage easily.REPLACE CONTINUED12. Install condenser fan (Figure 5, Item 3) onto standby motor shaftREPLACE CONTINUED23. Reconnect electrical wiring (Figure 6, Item 10) to standby motorFigure 7. Standby Motor Mount Bracket Bolts.Figure 8. Alignment Clearances.4. Tighten three bolts (Figure 7, Item 1) on inboard standby motorMAINTAINER MAINTENANCE STANDBY MOTOR (MTRC S02 ONLY) REPLACEFigure 1. Standby Motor Electrical Connection.5. Loosen two alternator mounting bolts (Figure 2, Items 1 and 2) and self-locking nutFigure 2. Alternator Removal.17. Remove two screws (Figure 1, Item 6) and washers23. Remove condenser fan (Figure 4, Item 3) from standby motor shaftFigure 4. Standby Motor Attaching Hardware Removal.Guide pulley around vibration absorber while lifting standby motor assembly.Figure 5. Standby Motor Assembly.The radiator coils damage easily. In order to install the standby motorFigure 6. Standby Motor Attaching Hardware Installation.Fan blades are sharp and can cut. Use gloves when handling fan bladesMounting Bracket Diagram13. Install new idler assembly shaft (Figure 8, Item 18) through idler pulleyFigure 8. Alternator Installation.23. Install strain relief (Figure 9, Item 11) and nut (Figure 9, Item 10)Figure 9. Standby Motor Electrical Connection.MAINTAINER MAINTENANCE MICROPROCESSOR CONTROL BOX (MTRC S01 ONLY) REPAIRREPAIR CONTINUEDFigure 2. MPC Box Relay Test.Figure 3. MPC Box Relays, Capacitors, and Fuses.5. Operate unit in accordance with normal operating procedures to verify proper operationREPAIR CONTINUEDFigure 5. MPC Box Fuses.Replace Time DelayFigure 6. MPC Box Resistor, Ribbon Cable, Time Delay, and Diode.Test Diode BlockPin layout and circuit diagramFigure 8. MPC Box Resistor, Ribbon Cable, Time Delay, and Diode.Replace MPC Circuit BoardFigure 9. MPC Board.13. Connect two electrical connectors (Figure 9, Item 17) to MPC circuit boardFigure 10. Microprocessor Control Display PanelTable 1. Microprocessor Configuration SettingsMicroprocessor Control Box Component IdentificationTable 1. Microprocessor Control Box Component Identification Continued.Figure 11. Microprocessor Control Box Back Wall and Bottom.Figure 12. Microprocessor Control Box Door and Forward Wall.Figure 13. Microprocessor Control Box Aft Wall.Hybrid Standby Panel Relay Replace (Overload Protector OL)REPAIR CONTINUED7. Remove two nuts and washers from the 1EHR or 2EHR relay and remove the relay.Shielded Ribbon Cable J12 ReplaceREPAIR CONTINUEDFigure 17. J12MAINTAINER MAINTENANCE MICROPROCESSOR CONTROL BOX (MTRC S02 ONLY) REPAIRTable 1. Microprocessor Control Box Component Identification Continued.Figure 1. Microprocessor Control Box Back Wall and Bottom.Figure 2. Microprocessor Control Box Door.Figure 3. Microprocessor Control Box.1. Wait five minutes to allow stored energy to dissipate from capacitorsFigure 4. Capacitors.1. Pull fuse holder (Figure 5, Item 1) up out of socketFigure 5. Resistor and Fuses.Replace Fuse F1Evaporator Heater Relay ReplaceFlashing Relay and Electric Motor Relay ReplacePanel Assembly Replace (Overload Protector (OL) and Motor Contactor (MC))Figure 8. Panel Assembly (OL and MC).7. Tag and remove four wires (Figure 9, Item 1) from top of MCFigure 9. Overload Protector and Motor Contactor.Replace Relay Board FuseReplace RelayFigure 12. Relay Test.Replace Relay BoardReplace Microprocessor (MPC) BoardFigure 14. Bolt Tightening Pattern.The logic board will be destroyed if either terminal A1 or A3 is grounded.Figure 16. Microprocessor Control Display Panel.Table 2. Microprocessor Configuration Settings.19. After all the proper settings are entered, move the main power (RS)Figure 17. MPC Board.MAINTAINER MAINTENANCE EVAPORATOR REPLACEFigure 1. Control Box.10. Tag and disconnect evaporator electrical connector (Figure 2, Item 1)Figure 2. Evaporator Cover and Drain Line Disconnect.Figure 3. 7/8-Inch Refrigerant Pipe Saddle Clamp.Figure 4. 1/2-Inch and 3/8-Inch Refrigerant Pipes.Steps 34 and 35 are for compartment 2 (aft) evaporator only.Figure 5. Evaporator Mounting Removal.Installation of compartment 1 (forward) and compartment 2 (aft)Figure 6. Refrigerant Piping StuboutLifting or moving heavy equipment incorrectly can cause serious injury.Figure 8. Evaporator Installation.Use wet rags on either side of soldering points in order to dissipate heatFigure 9. Evaporator Cover and Drain Line Installation.24. Install drain tubes (Figure 9, Item 12) onto elbowsFigure 10. Control Box Assembly.MAINTAINER MAINTENANCE EVAPORATOR THERMOSTATIC EXPANSION VALVE REPLACEFigure 1. Control Panel.Figure 2. TXV Replacement.When removing the TXV bulb, it is important to note the position of the bulb26. Solder equalizer line (Figure 2, Item 13) into TXVTable 1. R-404A Pressure Temperature Chart to Determine S .MAINTAINER MAINTENANCE CONTROL PANEL ASSEMBLY REPAIRFigure 1. Control Panel Toggle Switches.Replace Indicator Light Incandescent LampsFigure 2. Control Panel Indicator Light Incandescent Lamps.Replace Indicator LightsFigure 3. Control Panel Indicator Lights.Replace Alarm HornsFigure 4. Control Panel Alarm Horns.Replace Terminal BoardFigure 5. Control Panel Terminal Board.Replace Compartment ON/OFF SwitchesFigure 6. Control Panel ON/OFF Switches.Replace POWER ON/DOWN SwitchFigure 7. Control Panel POWER ON/DOWN Switch.Replace Resistive Heating ElementFigure 8. Resistive Heating Element.MAINTAINER MAINTENANCE POWER BOX (MTRC S01 ONLY) REPAIRFigure 1. Power Control Box Door.Replace Selector Switches S1, S2Replace Circuit Breakers CB1, CB27. Carefully pull circuit breaker bracket (Figure 3, Item 11), with circuit breakerFigure 3. Power Control Box Circuit Breaker.Replace Toggle SwitchFigure 5. Control Panel Wire Bundle.Figure 6. Power Box and Control Panel Assembly Door.Figure 8. Power Box Attaching Hardware.Figure 9. Control Panel Assembly Bolts.Figure 10. Positioning Forklift Entering Power Box.Figure 12. Top Power Box Mount Bolts.Figure 14. Electrical Box Cover.Figure 16. Power Box Door.Figure 18. Lifting Strap.Figure 20. Lifting Transformer from Power Box.Figure 22. Transformer U-Nuts.12. Install electrical box cover (Figure 14, Item 2) to electrical box15. Move power box into position on MTRCS.MAINTAINER MAINTENANCE POWER BOX (MTRC S02 ONLY) REPAIRFigure 1. Power Control Box Door.Replace Selector Switches S1, S2Replace Circuit Breakers CB1, CB26. Remove four screws (Figure 3, Item 7), lock washers (Figure 3, Item 8)REPAIR CONTINUEDFigure 4. Replace Relay.2. Unplug and remove relay (Figure 4, Item 2) from relay socketReplace Transformer TR1Figure 6. Power Box and Control Panel Assembly Door.Figure 8. Power Box Attaching Hardware.Figure 9. Control Panel Assembly Bolts.Figure 10. Positioning Forklift Entering Power Box.Figure 11. Bottom Power Box Mount Bolts.Figure 12. Top Power Box Mount Bolts.Figure 13. Power Box Removal.Figure 15. Removing TR1-X0 WiresFigure 16. Lifting Strap.Figure 17. Transformer Mounting Bolts.24. Slowly lift transformer out of power box by guiding it around wiresFigure 19. Removing Wires on Transformer Terminal Block.Figure 20. Transformer U-Nuts.7. Secure transformer (Figure 16, Item 2) to power box (Figure 17, Item 4)Figure 21. Lifting Power Box with Forklift.Figure 22. Top Power Box Mount Bolts.Figure 24. Control Panel Assembly Bolts.19. Close control panel assembly door (Figure 6, Item 2).MAINTAINER MAINTENANCEPOWER CABLE ASSEMBLIES REPAIRFigure 1. Connector Repair.11. Using contact crimp tool, locator, and die, crimp replacement contact (Figure 1, Item 9)23. Reconnect battery (WP 0053, Reconnect).MAINTAINER MAINTEANCE BATTERY BOX (MTRCS01 ONLY) REPLACE, REPAIRExercise caution when using tools on or around the battery.Figure 3. Battery Cables.12. Install negative (-) battery cable (Figure 3, Item 1) and secure negativeMAINTAINER MAINTENANCE BATTERY BOX (MTRC S02 ONLY) REPLACE, REPAIRReplace Battery CablesREPAIR CONTINUED12. Install replacement positive (+) battery cable (Figure 3, Item 2)MAINTAINER MAINTENANCE CAPACITOR BOX REPAIRFigure 1. Capacitor Box.Replace Capacitor Box Cover SealFigure 2. Capacitor Box Cover Seal.MAINTAINER MAINTENANCE DOORS REPAIRFigure 2. Prying Tool.Replace Emergency Escape Hatch GasketsWhile removing the gasket you can damage the emergency escape hatchFigure 5. Emergency Escape Hatch Inner Seal.9. Apply lubricant to back of new outer gasket (Figure 3, Item 4).MAINTAINER MAINTENANCE REFRIGERATION PIPING REPAIR4. If desoldering a joint on a valve, disassemble valve as much as possible1. Protect wiring harnesses and other components with appropriate heat shields.2. Remove access panels as needed to gain access to piping or fittings.MAINTAINER MAINTENANCE TORQUE LIMITSTable 3. Bolt Torque Values for U.S. Threads in Foot-Pounds.Table 4. Bolt Torque Values for Metric Threads in Foot Pounds.MULTI-TEMPERATURE REFRIGERATED CONTAINER SYSTEM (MTRCS) GENERAL WIRING REPAIRINTRODUCTION CONTINUEDWIRING DIAGRAMS, ELECTRICAL SCHEMATICS, AND REFRIGERATION SCHEMATICSMULTI-TEMPERATURE REFRIGERATED CONTAINER SYSTEM (MTRCS) PREPARATION FOR STORAGE OR SHIPMENTPREPARATION FOR STORAGE CONTINUEDCHAPTER 4 - SUPPORTING INFORMATION FOR MULTI-TEMPERATURE REFRIGERATED CONTAINER SYSTEM (MTRCS)MULTI-TEMPERATURE REFRIGERATED CONTAINER SYSTEM (MTRCS) REFERENCESINTRODUCTION FOR STANDARD MAINTENANCE ALLOCATION CHART (MAC)Maintenance functions are limited to and defined as follows:EXPLANATION OF COLUMNS IN THE MACEXPLANATION OF COLUMNS IN THE MAC CONTINUEDMULTI-TEMPERATURE REFRIGERATED CONTAINER SYSTEM (MTRCS) MAINTENANCE ALLOCATION CHART (MAC)Table 1. MTRCS Maintenance Allocation Chart Continued.Table 1. MTRCS Maintenance Allocation Chart Continued.Table 1. MTRCS Maintenance Allocation Chart Continued.Table 1. MTRCS Maintenance Allocation Chart Continued.Table 1. MTRCS Maintenance Allocation Chart Continued.Table 1. MTRCS Maintenance Allocation Chart Continued.Table 1. MTRCS Maintenance Allocation Chart Continued.Table 2. Tools and Test Equipment for MTRCS.MULTI-TEMPERATURE REFRIGERATED CONTAINER SYSTEM (MTRCS) EXPENDABLE AND DURABLE ITEMS LISTTable 1. Expendable and Durable Items List for MTRCS Continued.Table 1. Expendable and Durable Items List for MTRCS Continued.Table 1. Expendable and Durable Items List for MTRCS Continued.MULTI-TEMPERATURE REFRIGERATED CONTAINER SYSTEM (MTRCS) MANDATORY REPLACEMENT PARTS LISTTable 1. Mandatory Replacement Parts List for MTRCS Continued.MULTI-TEMPERATURE REFRIGERATED CONTAINER SYSTEM (MTRCS) ADDITIONAL AUTHORIZATION LIST (AAL)Table 1. Additional Authorization List (AAL) for MTRCS
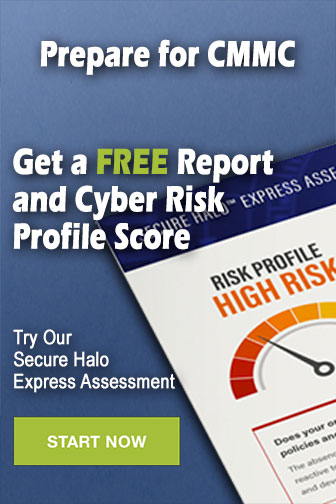